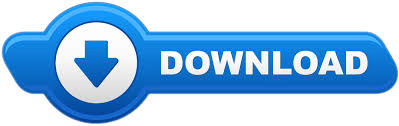
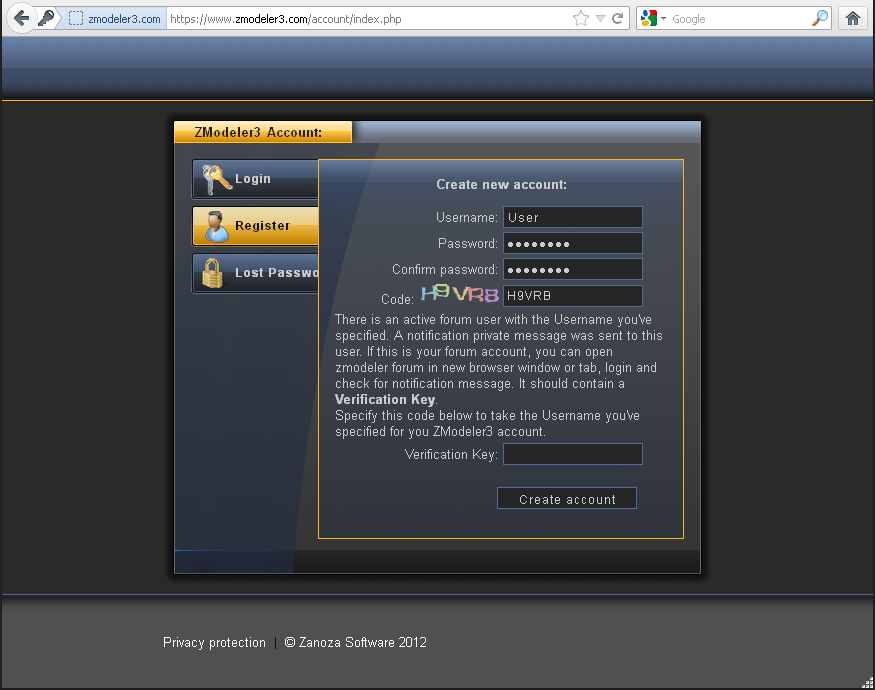
(Mouse over it to see all controls of the step-building) So make yourself ready, adding vertices is just a simple mouse click while adjusting vertices or creating polys out of them requires 1 to 3 keyboard keys + mouse click. Yes, one by one, and you will have to manually place hundreds of it. We will do this by placing vertices one by one. It should be taken into consideration that excessively low back pressure causes unstable metering due to the trapping of air and excessively high back pressure causes drooling from the nozzle and prolongs the plasticization time.Now we can finally start modelling the mesh. Occurrence of jetting, flow marks, flash, burning, etc.Ĥ.7 Screw Rotational Speed and Back Pressureįrom the standpoint of temperature variance of molten resins, theoretically it is desirable that screw rotational speed be lower and the back pressure be higher, but the following parameters are practical from the productivity point of view:Įxample screw rotational speed / back pressure:

When the injection speed is not appropriate, the following problems may occur:

When the mold temperature is set at temperatures as low as 30-40☌ in order to shorten the molding cycle, the following points should be taken into account: Moldings which require mirror surfaces are often molded at a mold temperature as high as 120☌. For example, in case of moldings used in elevated temperature, mold temperature must be higher than the application temperature, or molded products must be annealed in order to prevent dimensional change during use. 4-4 Discoloration range at elevated temperatureĪlthough the normal mold temperature of DURACON is 60-80☌, the actual mold temperature should be determined in consideration of properties of moldings, surface appearance, dimensional change in use, molding cycle time and other factors. 4-4 The permissible retention time is determined by discoloration rather than deterioration of properties.įig. Although the discoloration slightly varies with grades, the general discoloration limit for DURACON M90-44 is shown in Fig. The discoloration of a molding is related to the material temperature and retention time in the cylinder of the molding machine.
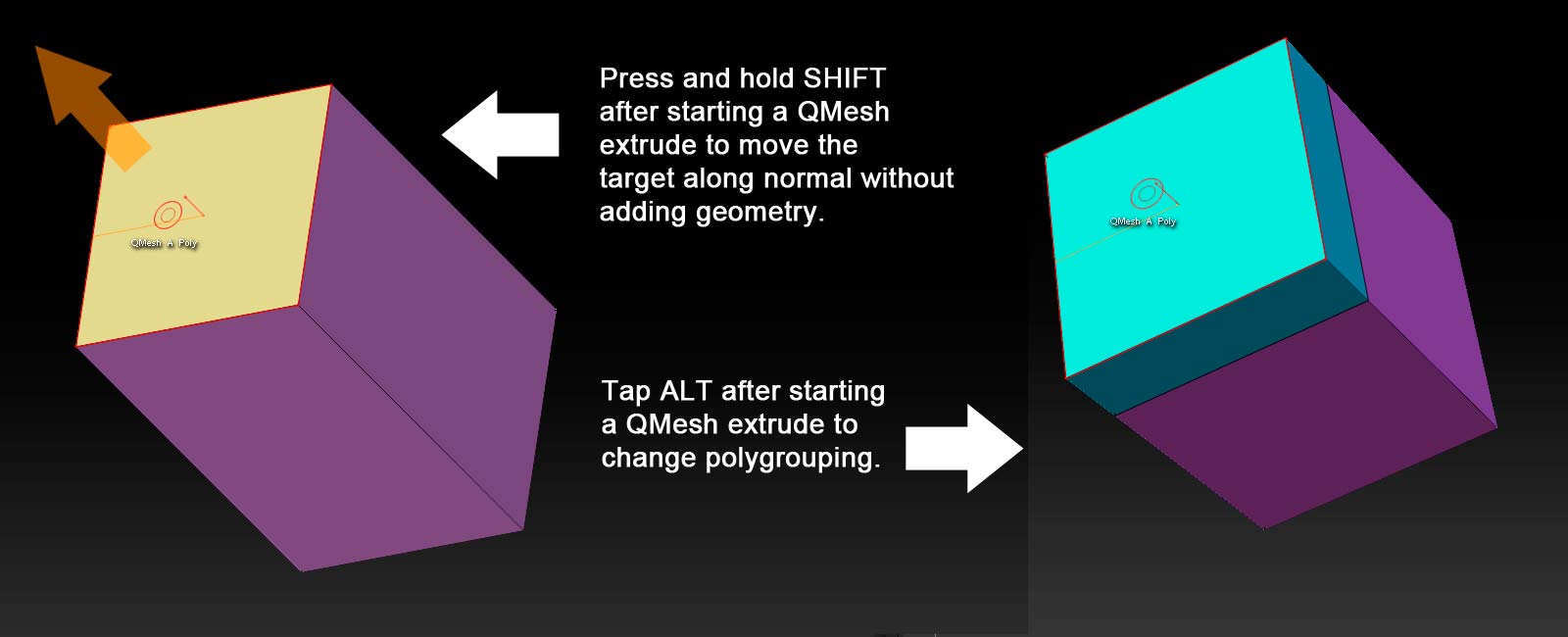
Too low a material temperature: inclusion of incompletely plasticized material.Too high a material temperature: decomposition and discoloration of the material.When the material temperature is not appropriate, the following problems may result: An example temperature distribution of the cylinder is shown below, and it is recommended that the temperature be directly measured by a thermometer inserted into the block of molten material as it exits the nozzle.Ĭonfiguration example of cylinder temperature: The material temperature is generally set 10-15☌ higher than the cylinder temperature (front section). The melting point of DURACON® POM is approximately 165☌, but from the practical point of view a material temperature of 190-210☌ (if possible 200-210☌) is appropriate. Standard Conditions Predrying Condition Setting Molding Cycle Countermeasures for MDĤ.3.1 Example Temperature Distribution of the Cylinder Home > Technical Support > Molding Technology > Molding Technology for DURACON(R) POM Molding Conditions / Condition Setting Contents
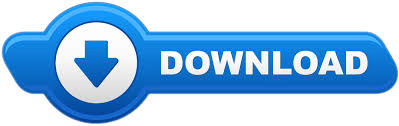